Compliance
Cleanroom Control: How to Improve Predictability and Maintain Compliance
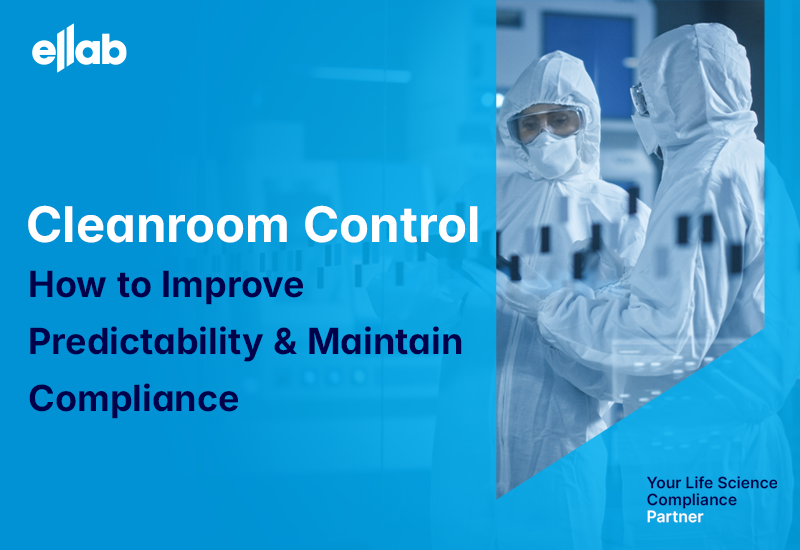
Is your cleanroom truly in control, or are early warning signs slipping by unnoticed? Sensor drift, calibration delays, and subtle temperature spikes can quietly push you out of spec. Let’s explore what reliable, sustained control looks like and how to achieve it.
As regulatory expectations evolve and operational risks become more complex, improving cleanroom control requires more than traditional compliance: It’s time to adopt a more proactive, holistic, and data-driven approach.
So, what does “cleanroom control” really mean, and how can you be sure you’re maintaining it? In this blog post, we’ll explore what effective cleanroom control and predictability look like, some early warning signs, and how to ensure your cleanroom remains audit-ready at all times.