Rent the Best the World of Validation has to Offer
- Complete turn-key or supplemental rentals
Ellab’s flexible services include the ability to cover and compensate almost any request, Ellab’s rental service stands ready to provide the necessary equipment.
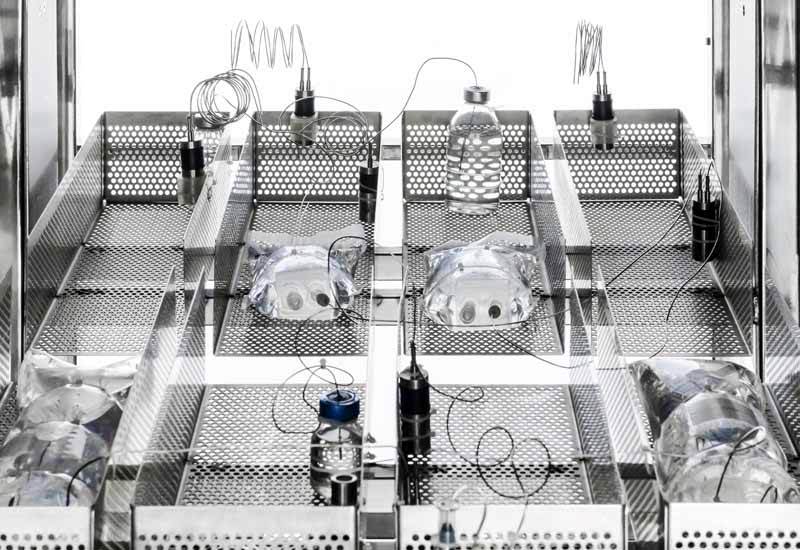
Data Logger Rentals for Validation Activities and Equipment Qualification
Data loggers rentals are a great option for new and existing customers, whatever the need:
- When you quickly need to respond to a situation
- When you would like to experience a product before purchasing
- When you need additional devices while equipment is being calibrated
- When you have a spike in mappings and require more equipment
- When you have annual projects that only last 1-2 months
As an existing customer, renting can also be a great way for you to ramp up equipment for requalification during shutdown seasons – without the additional costs that come with maintaining equipment post project.
Due to our large rental inventory, we can quickly respond to any rental request, allowing your process to remain smooth and efficient.
Wireless data-loggers or a thermocouple-based solution?
Both systems can measure temperature, humidity, pressure, CO2, vacuum, and conductivity. Additionally, both systems utilize the same software, giving you the opportunity to incorporate both systems in the same project if necessary.
Rent the Most Innovative Wireless Data Loggers
When wireless rental data loggers are the preferred choice for temperature mapping equipment, Ellab offers a wide variety of solutions for many applications. TrackSense® data logger rentals are the perfect solution for any high-volume or application-specific study, that are only performed once or twice a year. For example, summer and winter warehouse qualifications often require a large quantity of wireless data loggers and would, therefore, be the ideal rental solution.
We cover a wide scope of measurement parameters and each of our sensors are specifically designed to meet necessary standard requirements for individual qualification and validation processes. Ellab’s TrackSense® wireless sensors are made of 316L stainless steel, PTFE, or a mix of both. The wireless sensors measure temperature, pressure, RH, CO2, vacuum, and conductivity.
Common rental applications:
- Autoclaves
- Depyrogenation
- Lyophilization
- Stability chambers
- Warehouses
Wireless Data-Logger rental package includes:
✔ Rental laptop
✔ ValSuite® software installed (Optional Validation Package available)
✔ Master Reader station to program / read loggers
✔ Requested number of wireless data-loggers and sensors
✔ Battery & Calibration Certificate included for each unit
Rent our Modern Thermocouple System
Ellab also offers a wired thermocouple rental system, the E-Val™ Pro Plus. Our rental thermocouple system meets FDA/GAMP guidelines, is compact and light, making it easy to transport between tests. Operators have the option of renting thermocouples from Ellab or use their own thermocouples by renting our smart USB connectors.
Our smart USB connectors allow customers to connect their own thermocouples to the E-Val Pro Plus module and benefit from the cold-junction compensation that is stored individually in each unit. Ellab thermocouples offer a ±0.1°C accuracy for most applications but are typically more accurate in moderate applications.
The E-Val Pro Plus thermocouple system rental measures temperature, but can also measure the same parameters as the TrackSense Pro wireless data loggers; pressure, RH, CO2, vacuum, and conductivity by using data logger sensors in conjunction with the E-Val Pro Plus thermocouple system sensor interface.
Common applications for a rental thermocouple system:
- Autoclaves
- Refrigerators
- Freezers
- Stability chambers
- Ovens
Thermocouple System rental package includes:
✔ Rental laptop
✔ E-Val Pro module (up to 40 channels per unit)
✔ ValSuite® software installed (Optional Validation Package available)
✔ USB screw terminals or sealed thermocouples;
– the USB screw terminals allow customers to use their own thermocouples
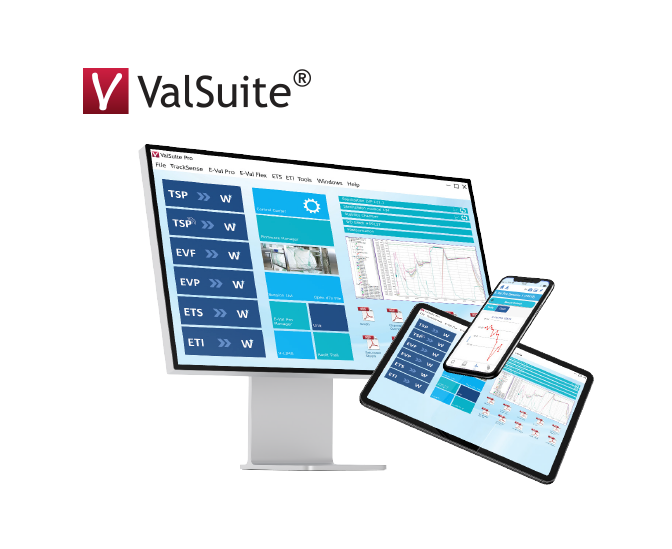
Intuitive ValSuite™ Software
Rental of wireless data loggers or a wired thermocouple system both include the intuitive FDA 21 CFR Part 11 compliant Valsuite® Pro validation software. ValSuite offers several reports to be configured once data is collected as well as a wide range of reporting features specific to validation and qualification processes. ValSuite also has a unique Windows Security compatibility, making it a truly a safe and reliable software that meets industry guidelines.
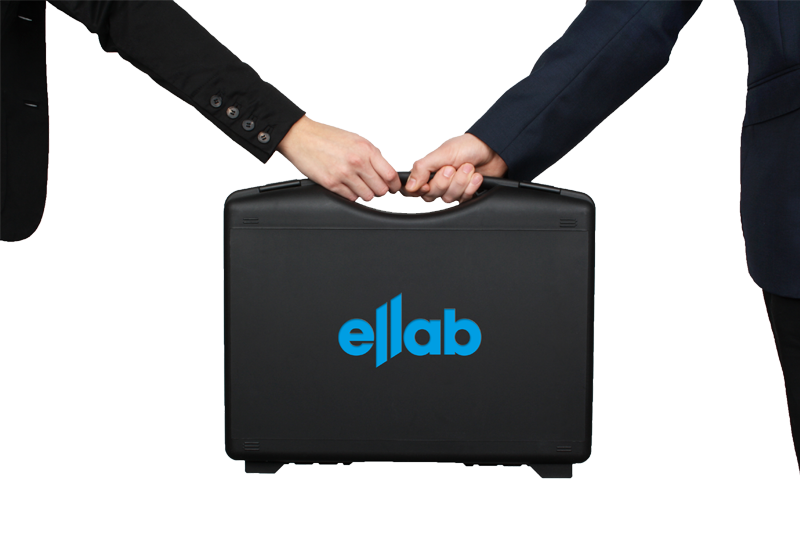
Why Choose Ellab?
Supplemental and Turn-key Rental Systems
Ellab offers sensor types for a variety of environmental parameters including:
temperature, relative humidity, pressure, CO2, vacuum and conductivity. Pre and Post-Calibration services are also available, allowing operators to do their job without having to worry about performing their own calibrations on-site.
With our huge inventory of rental equipment maintained to the highest standards, we are ready to accommodate rentals for projects of any size or duration.